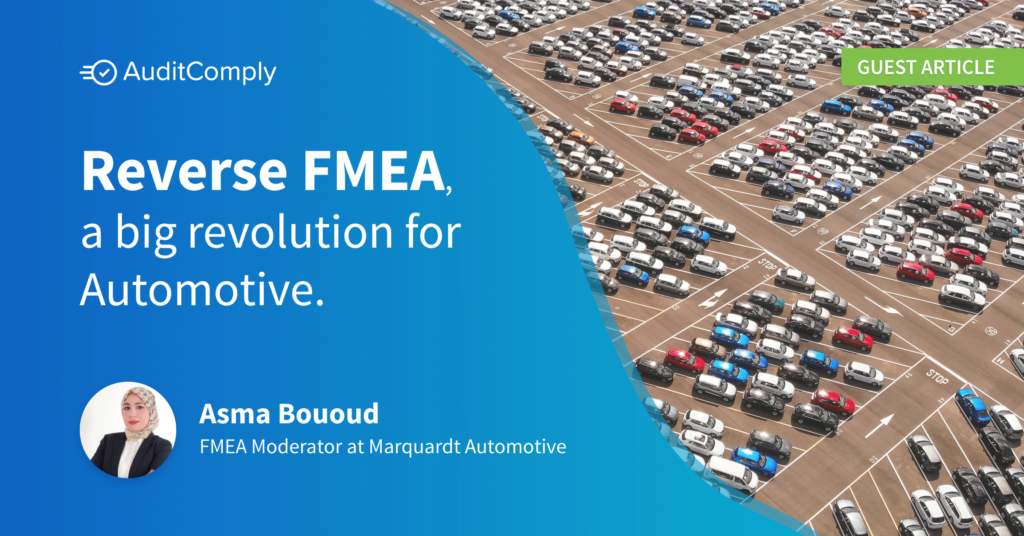
Reverse FMEA (Failure Modes & Effects Analysis) is one of the most recent tools used for continuous improvement, which I personally consider a revolution in the field of risk management. Reverse FMEA is used to enhance the PFMEA, since it’s based on on-site observation. However, before we approach Reverse FMEA further, let’s make sure we understand more about FMEA.
It’s a fact that failures are meant to happen, but imagine if we could find a way to look into the future and predict where a failure might occur, how they happen, how often then might occur and what their consequences may be. With such a tool, life will be much easier, costs would be more controllable and your company will be the perfect example for risk management effectiveness.
This is what FMEA is used for, one of the most popular tools used for risk analysis, especially for the automotive industry. The FMEA definition according to AIAG & VDA Handbook is a team-oriented, systematic, qualitative, analytical method intended to:
-Evaluate the potential technical risks of failure of a product or process
-Analyze the causes and effects of those failures
-Document preventive and detection actions
-Recommend actions to reduce risk
FMEA methodology is based on the identification of three elements, Failures (Failure causes), Failure modes and Effects. Failure is any potential / actual error or defect which can affect the customer, the end user or the legal requirements, failure mode is the manner in which an item could fail to meet or deliver the intended function and effects are consequences of failures, this relationship can be explained by the following graphic known as a “Failure Net”:After the construction of the failure net, Effects and Failures will be rated on the basis of three different scales: Occurrence, detection and Severity (O,D & S) , by multiplying the three ratings, we get to the Risk Priority Number (RPN).
What is the definition of each rating?
Severity (S) evaluates the severity of each failure effect, it’s value is between 1 (very low or with no effect) and 10 (very high, affects the user safety or legal requirements in general). Occurrence (O) evaluates the probability of a failure cause to appear. Detection (D) evaluates the detection probability of a failure cause, failure mode or effect.
Severity or short S evaluates the severity of each failure effect from a customer’s point of view, it’s value is between 1 (very low or with no effect) and 10 (very high, affects the user safety or legal requirements in general). Occurrence or short O evaluates the probability of a failure cause to appear, and detection or short D evaluates the detection probability of a failure cause, failure mode or failure. Both of O and D values are also between 1 and 10, according to this rating, the maximum value of RPN is 1000.
Organizations define their own custom thresholds to determine what should not be exceeded, else risk exists and they need to define further actions to guarantee more prevention or detection for failures. It’s very important to know that ratings for occurrence and detection are given based on the consideration of the defined actions. We can guarantee a low occurrence by defining “Poka Yoke” which is a mechanism that helps an equipment operator avoid failures.
Low occurrence can also be guaranteed through efficient training programs. The organization’s know-how of the Product / Process itself is also a significant factor for the occurrence evaluation. For detection, the rating is according to the means of control, for example, camera control, visual control. A low detection can only be guaranteed by an automatic and effective control method. Visual controls are highly rated in FMEA even with “Well trained operators” or with many visual control stations. The severity rating is fixed and cannot be changed, to reduce the overall RPN, we can only work on the Occurrence or Detection of on both of them.
Introducing Reverse FMEA
Despite the fact that FMEA is considered as one of the most powerful tools for risk prevention, FMEA is currently being performed in meeting rooms, based on multidisciplinary teams brainstorming away from the reality of the field and real-life manufacturing situations. In order to confront FMEA outputs with real-life situations, the Reverse FMEA method was released.
What are the outputs of Reverse FMEA?
With Reverse FMEA, we can identify new risks (new failure causes, new failure modes etc). This method allows us to also enhance the FMEA process by a re-rating of our failures.
Reverse participation

Similar to FMEA, Reverse FMEA is conducted by the presence of a multidisciplinary team (quality, process, industrialization, safety etc.) and led by someone who is responsible for the respect of FMEA/ Reverse FMEA methodology.
How is Reverse FMEA performed?
Until now, there has been no normative requirement for the obligation of Reverse FMEA. However this is changing. Many of our customers ( General Motors, PSA, Continental, Renault) are requiring their suppliers to perform Reverse FMEA. As a result, many organizations started including it in their standards, not only to satisfy customers but also because this method has shown to be highly effective.
The Reverse FMEA’s team selects the production line where the Reverse FMEA will take place, preparing the necessary inputs (Documentation, PPM data, Flowchart, PFMEA, Control Plan, Work Instructions, Drawings etc). Regarding the “how to”, I would say there is no specific way to do it, some customers are requesting specific procedures but in general, most organizations are defining their own methodology in their FMEA standards. It is recommended users follow a Reverse FMEA checklist and to verify the included points, here is some examples:
-Verify the coherence between documentation (Flowchart, FMEA, Control Plan) and the existing production line
-Verify the existence/ maintenance of PFM
-EA measures (preventive actions, detection actions) for identified failures. Identify new risks by the creation of failure modes at workstations and testing of detection methods’ effectiveness.
-Re-rate occurrence / Detection according to the production Data and the team’s observation
The team’s observation and the new risks identified are then documented so they can be used as inputs for PFMEA reviews. All new risks or measures must be added to the FMEA as well as the new ratings in order to guarantee that your FMEA’s are up to date and reflect the reality of field operations.
Reverse FMEA was not only a revolution in the world of FMEA, the new AIAG & VDA FMEA Handbook (described as “a long awaited publication”) was released in June 2019, marking a transformation for risk management in automotive. This new edition incorporates best practices from both AIAG and VDA methodologies and is definitely worth a read.
About the author

Asma Bououd, a Mechanical Engineer who graduated from the National Higher Engineering school of Tunisia, is currently the FMEA Moderator at an automotive manufacturing company. This is Asma’s second experience in FMEA moderation. For Asma, FMEA is not only a career choice, it’s a passion.