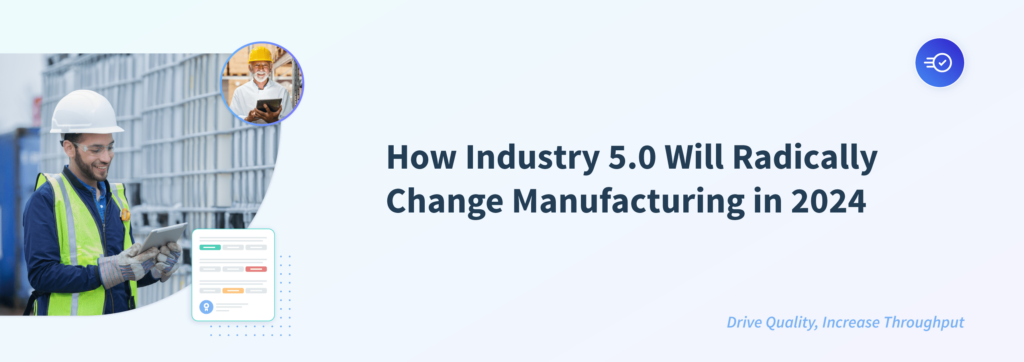
The Dawn of Industry 5.0: Navigating the Future of Manufacturing in 2024
The manufacturing sector has always been at the forefront of technological revolutions. From the steam engines of the First Industrial Revolution to the automation systems of Industry 4.0, each phase has brought about transformative changes. As we stand at the cusp of 2023, the manufacturing world is abuzz with the promise of Industry 5.0. This new era is not just about machines and automation; it’s about the harmonious integration of human creativity with advanced technology.
Industry 5.0 and the Imperative of Digital Transformation
Digital transformation varies across industries, manifesting as either a gradual integration or a comprehensive revamp to anchor digital technologies and software at the core of operations. In the realm of manufacturing, the latest technological breakthroughs have paved the way for digitally augmenting processes, encompassing nearly every facet of sourcing, production and distribution.
Industry 5.0, often referred to as the fifth industrial revolution, marks a significant shift from the previous era of automation and data exchange (Industry 4.0) to a more human-centric approach to manufacturing and production. While Industry 4.0 focused on the Internet of Things (IoT), robotics, and automation, Industry 5.0 emphasizes the collaboration between humans and machines, aiming to harness the best of both worlds. At the heart of Industry 5.0 is digital transformation. This is not just about adopting new technologies but about fundamentally changing how businesses operate and deliver value to their customers.
Industry 5.0 Is Designed to Empower Not Replace, Humans
Human Centric Approach / Frontline Worker Focus: The primary distinction of Industry 5.0 is its focus on the human element. While Industry 4.0 emphasized automation and the Internet of Things (IoT), Industry 5.0 seeks to bring the human touch back into the production process. This means that tasks will not be solely relegated to robots; instead, humans and machines will collaborate more closely, leveraging the strengths of both.
Customization of Mass Production: One of the most significant shifts in Industry 5.0 is the move from mass production to mass customization. With the aid of advanced technologies like Artificial Intelligence (AI) and 3D printing, manufacturers can now produce goods tailored to individual customer preferences without compromising on efficiency or cost.
Sustainable Manufacturing: Environmental concerns are taking center stage in Industry 5.0. Manufacturers are increasingly adopting sustainable practices, from sourcing raw materials to waste management. The emphasis is on creating a circular economy where resources are reused and recycled, minimizing environmental impact.
Enhanced Quality Management: Quality management in Industry 5.0 is not just about meeting standards; it’s about exceeding them. With the integration of real-time data analytics, manufacturers can monitor and optimize processes instantaneously. This not only ensures product quality but also reduces wastage and improves efficiency.
Decentralized Production: The rise of smart factories in Industry 5.0 means that production is no longer confined to large centralized facilities. Instead, smaller, decentralized units equipped with advanced technologies can produce goods closer to the end consumer. This reduces transportation costs and lead times, offering a competitive advantage.
Upskilling the Workforce: With the advent of Industry 5.0, there’s a pressing need to upskill the workforce. While automation will handle repetitive tasks, humans will be required to manage and work alongside these systems. This necessitates training in areas like AI, robotics, and data analytics.
Digital Twins and Virtual Reality: Digital twins, virtual replicas of physical assets, will play a pivotal role in Industry 5.0. They allow manufacturers to simulate and test processes in a virtual environment before implementation. Coupled with Virtual Reality (VR), this offers unparalleled insights and optimization opportunities.
The importance of digital transformation in Industry 5.0 cannot be overstated. It is the bridge that connects advanced technologies with human ingenuity, ensuring businesses remain competitive, innovative, and responsive to ever-evolving market demands. In essence, digital transformation is the catalyst that will drive the success of Industry 5.0, shaping the future of manufacturing and production.
AuditComply and Industry 5.0: A Harmonious Integration
In the era of Industry 5.0, where the emphasis is on human-machine collaboration, tools like AuditComply play a pivotal role. AuditComply, a comprehensive risk and performance management platform, facilitates seamless integration of advanced technologies with human expertise. By providing real-time insights, streamlined audit processes, and data-driven decision-making capabilities, AuditComply empowers organizations to navigate the complexities of Industry 5.0.
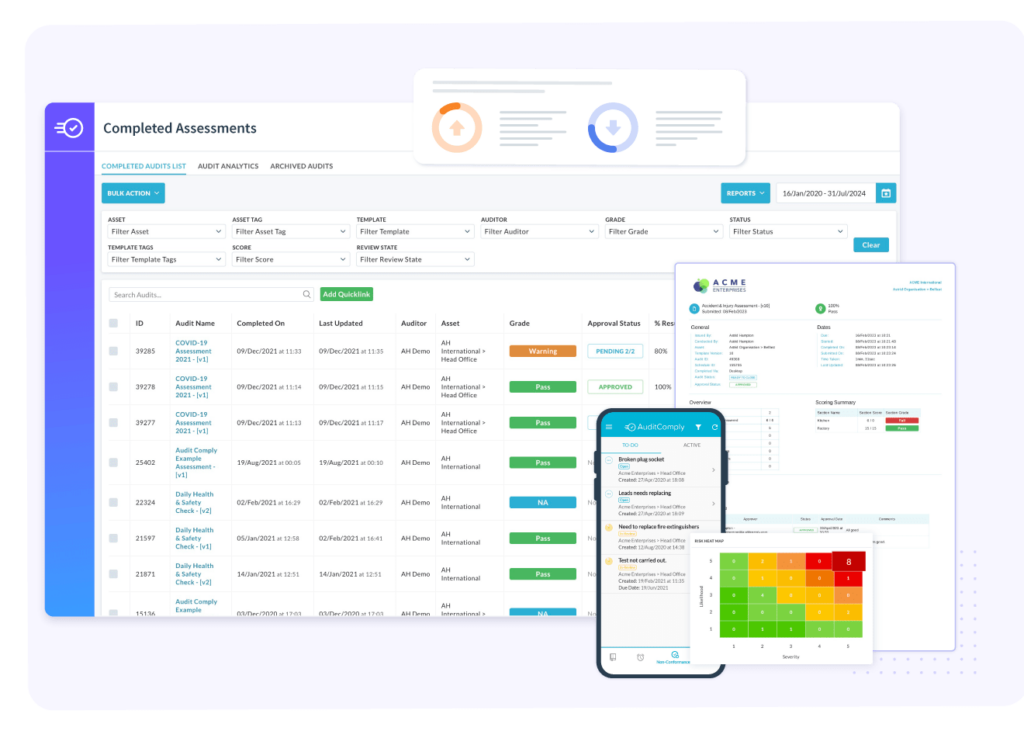
Its ability to ensure compliance, enhance operational efficiency, and promote continuous improvement aligns perfectly with the objectives of Industry 5.0. As businesses strive to combine human creativity with technological advancements, platforms like AuditComply become indispensable in bridging the gap and driving forward the vision of a collaborative and efficient future.
If you’d like to learn more about how AuditComply can assist in your digital transformation journey, request a demo today!